No mundo dinâmico da beneficiamento de arroz, encontrar desafios operacionais é inevitável. Este artigo mergulha no reino das falhas comuns que podem surgir em plantas de rice milling machine e fornece métodos eficazes de resolução de problemas.
Compreender e abordar estas questões é essencial para manter a eficiência e a produtividade das operações de moagem de arroz. Desde soluços mecânicos até desafios relacionados ao processo, exploramos soluções práticas para manter seu moinho de arroz funcionando perfeitamente.
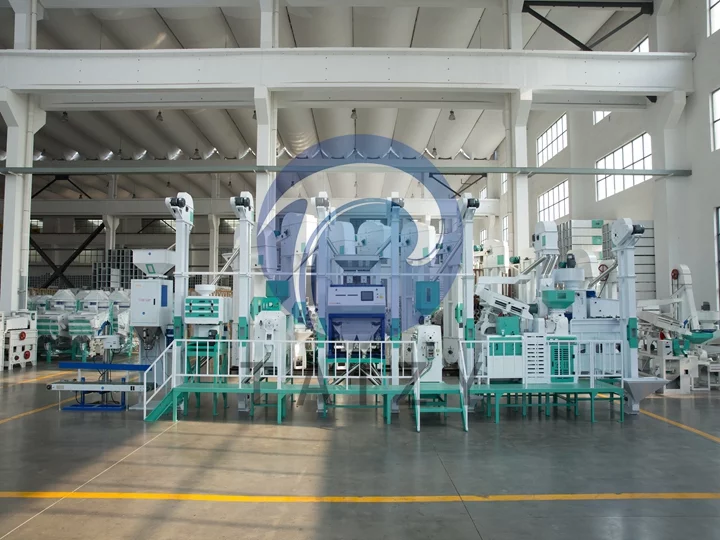
1. Despedregadora de Arroz em Casca
Há muito grão na pedra
1. Retire a ardósia e sele os orifícios da escama de peixe na placa selecionada.
2. O material está descentralizado.
3. O fluxo de material é excessivo ou insuficiente.
A pedra tem dificuldade em ser descarregada
1. Corte irregular.
2. A largura da ardósia não é nivelada.
3. Movimento desigual da ardósia.
4. Vibrações severas na máquina.
Muito areia no arroz
1. O movimento do corpo da peneira é anormalmente pronunciado.
2. Volume de sucção inadequado, fazendo com que o material não suspenda.
3. Configuração de velocidade incorreta.
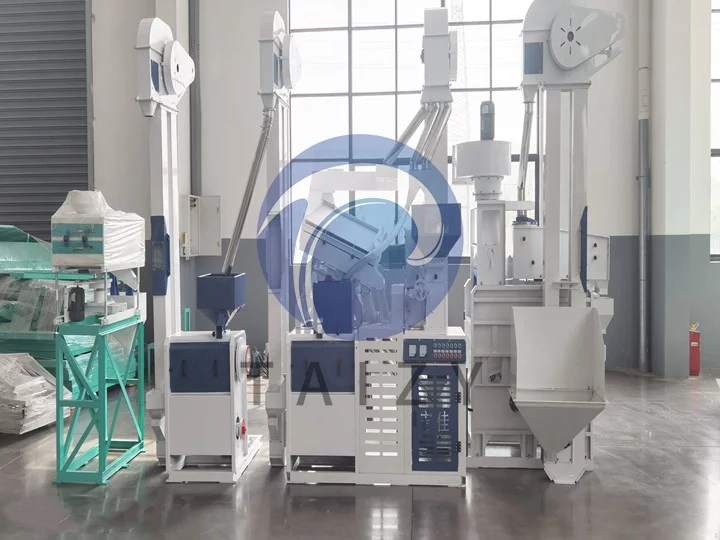
2. Descascador de Arroz em Casca
A taxa de descascamento é baixa
1. Alimentação excessiva.
2. Humidade excessiva no grão cru.
3. Pressão insuficiente no rolo de borracha.
A taxa de quebra é alta
1. Pressão excessiva entre os rolos.
2. Reciclagem excessiva de arroz em casca.
Paragem súbita
1. Obstrução de arroz no rolo de borracha.
2. Obstrução entre os rolos de borracha.
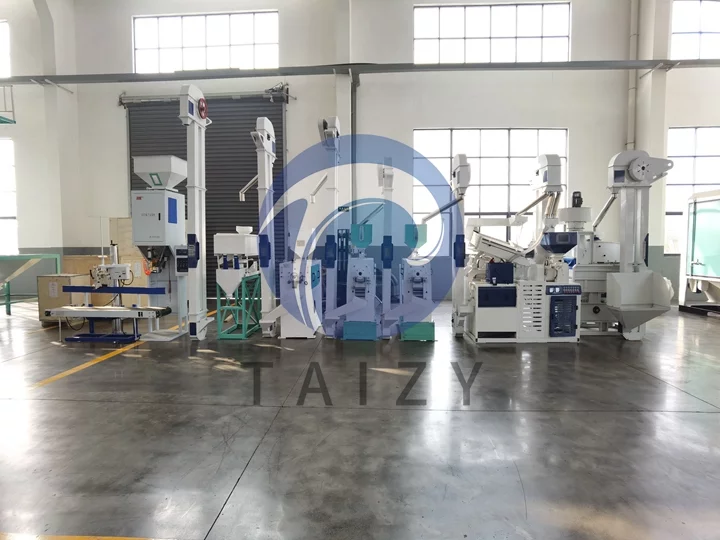
3. Separador de arroz em casca por gravidade
Vibração forte ou ruído elevado
1. Porcas de fixação e fixadores soltos.
2. A contraporca na haste de tração não está segura.
3. Posicionamento incorreto dos dois conjuntos de suportes ou falta de um rolamento.
4. O parafuso externo que liga a caixa de separação e o corpo de suporte não está apertado, resultando em folga excessiva entre a dobradiça e o pino.
5. A correia de transmissão está excessivamente tensa e o eixo do motor não está paralelo à linha central do fuso.
6. Ocorrem colisões entre a entrada/saída e o tubo de material.
As separações das diferentes camadas não são uniformes
1. Cobertura desigual de arroz em casca.
2. Aperto solto dos parafusos numa camada específica da superfície da peneira, levando à descolagem da placa de separação.
3. Impacto da alimentação, fazendo com que cascas grandes se desviem para o lado.
4. Fluxo de material excessivo.
5. Ângulo inadequado.
6. Fixadores soltos na ligação entre o corpo de suporte e a tração, a estrutura do assento do eixo pequeno e o corpo da caixa, perturbando o paralelogramo e causando desordem.
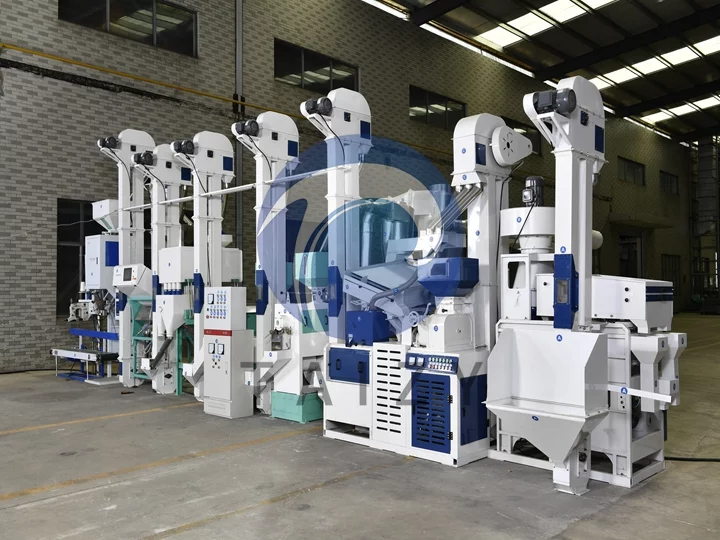
4. Moinho de Arroz
A produção diminui significativamente
1. A hélice de parafuso apresenta desgaste significativo.
2. Observa-se um desgaste severo no rolo de areia.
Arroz partido em excesso
1. Ligação irregular da peneira de arroz.
2. Ligação deficiente entre o rolo de areia e a hélice.
A precisão do produto acabado é desigual
O rolo de areia apresenta desgaste significativo.
Muito farelo no arroz branco
Os orifícios da peneira de arroz estão bloqueados.