Paddy processing refers to the production process of processing paddy into rice. The process is based on the requirements and characteristics of rice processing, selecting appropriate processing equipment, and combining the production process according to a certain processing sequence. It can be divided into cleaning, hulling, and separation of hulling, rice milling, and finished product finishing. This article mainly talks about cleaning the paddy.
Purpose of Cleaning
The production, harvesting, transportation, and storage of paddy may be mixed with some impurities. If these impurities are not removed in advance, it is easy to bring great harm to processing. If the paddy is mixed with hemp rope and various straws, it is easy to cause the blockage of the conveying pipeline and the feeding machine in the production, which will hinder the normal production and reduce the technological effect and processing capacity of the equipment. If the paddy is mixed with hard impurities such as sand, stone, metal, etc., it is easy to damage the equipment and even cause accidents such as dust explosion. If the paddy contains soil and dust, it will easily pollute the environmental sanitation of the workshop, and endanger human health. If impurities in the paddy are not cleaned and mixed into the finished product, the purity of the product will be reduced and the quality of the rice will be affected greatly. Therefore, removing impurities is an important task in rice processing.
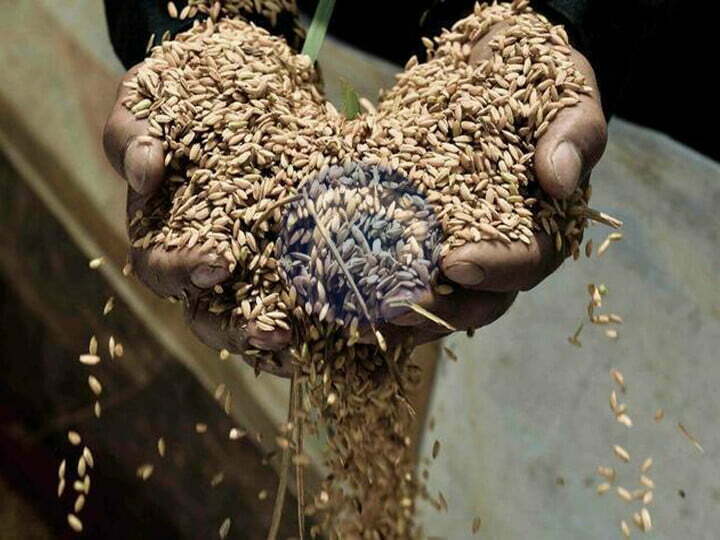
Types of Impurities in Paddy
The impurities in paddy are various, some are heavier than it, some are smaller, and some are lighter than paddy.
classification according to their chemical properties:
The impurities in paddy can be divided into inorganic impurities and organic impurities. Inorganic impurities include soil, sand, cinder, bricks and tiles, glass fragments, metal objects, and so on. Organic impurities include rice husks, tares, straws, heterogeneous grains, seeds of wild plants, as well as sprouts and diseased grains with no edible value.
According to its particle size, it can be divided into large, medium and small impurities.
classification according to the nature of impurities in paddy:
Large impurities: it is remaining on the sieve with a diameter of 5.0 mm.
Intermediate impurities: it can pass through a circular hole sieve with a diameter of 5.0 mm, but cannot pass through a round hole sieve with a diameter of 2.0 mm.
Small impurities: it can pass through a 2.0 mm diameter round hole sieve.
According to its relative density, it can be divided into light impurities and heavy impurities
Light impurity: relative density is smaller than that of paddy.
Heavy impurities: relative density greater than that of paddy.
Cleaning Method
When cleaning impurities in the paddy, it is necessary to select a reasonable cleaning method and equipment according to the weight and quantity of the impurities in the paddy, and which can give full play to the efficiency of the equipment. According to the physical characteristics of various impurities, remove them by the principle of easy first and then difficult. The removed impurities should be classified separately for centralized processing. A variety of impurity removal methods are carried out simultaneously to achieve the purpose of complementing each other.
The cleaned paddy is the net rice, and the total amount of impurities cannot exceed 0.6%, the content of sand and stone is not more than 1 grain/kg, and the barnyard is less than 130 grains/kg.
There are many equipment for cleaning impurities in paddy, and the methods for cleaning impurities are also different. Therefore, if the process effect, production effect, and existing problems of various cleaning equipment can be correctly evaluated, which will have a very important meaning in improving operation technology and promoting production. The indicators for evaluating the process effect of cleaning equipment are the net grain extraction rate and the impurity removal rate. Impurity removal rate = (impurity content before cleaning)-(impurity content after cleaning content before cleaning × 100%. When calculating the impurity removal rate, it should be calculated separately according to the various impurities removed (large impurities, small impurities, light impurities, tares, etc.). Net grain extraction rate = net grain volume after cleaning/net grain volume before cleaning × 100%.